As demand continues to grow for fast, reliable, mission-critical electronics for aerospace, battlefield gear, avionics, defense, energy, industrial, and other harsh-environment applications, electronics fabricators are incorporating fiber optics and fiber-optic connectors into their printed circuit board (PCB) designs.
Fiber-optic components on PCBs provide higher bandwidth connectivity, are stronger than traditional components, and typically take up less space on a PCB. They don’t need a power boost for extended signal travel and are also less prone to electromagnetic interference, helping ensure PCB longevity. After initial installation, the fiber-optic connections require little maintenance. 12 Port Patch Panel

Using fiber-optic components does require special handing and care. But particular attention is necessary for proper cleaning during installation. Cleanliness of the connections is imperative for the PCB, and ultimately the finished electronic device, to perform without fault.
Contamination is one of the main causes of fiber-optic failure. Dirty end-faces (fiber connections) can cause many problems ranging from intermittent operation to a complete breakdown. Cleaning fiber end-faces ensures the reliability and longevity of the PCBs.
End-face contamination can’t be seen with the naked eye. Common contaminants such as microscopic dust particles, salt, or fingerprint oils typically are only seen with a specialized 200x or 400x digital inspection scope (see Fig. 1). Even new end-faces, still in their original packages from the factory, are typically contaminated with packaging debris and off-gassing vapors from plastic endcaps intended to protect the end-face from damage prior to installation. Therefore, it’s prudent to clean and inspect all fiber-optic end-faces prior to connecting.
Digital inspection scopes are commonly used to inspect end faces and ensure International Electrotechnical Commission (IEC) compliance. The IEC published the fiber end-face specification 61300-3-35 to guide the fiber-optic industry in identifying the types of contaminants on end-faces and how to best remove them. Section 5.3 of IEC 61300-3-35 recommends using a three-step process of inspect, clean, inspect for end-faces.
Most digital inspection scopes use automated, software-driven algorithms to accurately compute the size, area, and location of end-face contaminants. The total inspection process, using a digital scope, takes less than five seconds for an accurate analysis. Also, most modern digital scopes capture an image of the end-faces, allowing the inspector to see and document the end-faces’ condition both before and after cleaning.
Particulate contamination adheres to end-faces by electrostatic attraction and can remain on the fiber end-faces for weeks or even months until the static charge finds a conductive path for it to dissipate. Using a specially engineered fiber-optic cleaning fluid quickly dissipates the static and makes it easier to wipe away the particulate. The cleaning fluid also dissolves any oils found on the end-faces. Wet-to-dry cleaning can be used with any tool you choose—whether it is a clicker, stick, or wipe.
To wet-to-dry clean, carefully apply a small amount of high-purity cleaning fluid on the corner of a dry, lint-free wipe. Starting at the wet section, slowly swipe the end-face toward the dry section of the wipe.
If using a cleaning stick, wet the tip of the stick directly from the dispenser cap of the can or touch it to a cleaning wipe moistened with cleaning fluid. Then, insert the stick tip into the end-face to clean.
As with water-based cleaners, IPA may explode or catch on fire when left on a highly energized fiber end-face. IPA also frequently leaves a hazy film behind when it dries. So instead, use a fast-drying, high-purity fluid engineered specifically for cleaning fiber-optics.
Beware of pre-saturated cleaning materials. Pre-saturated wipes and cleaning sticks often contain microscopic plasticizer contaminants drawn from their plastic packaging, which typically transfers to the end-face during cleaning.
Salts, usually left from skin oil, are often not fully removed with cleaning fluids alone. While cleaning fluids rinse away particulates and oils, they tend to leave a white salt residue behind that can be very difficult to remove. Adding mechanical cleaning action with a cleaning wipe or stick helps scrub the residue away. There are two primary methods to properly clean fiber-optic end-faces: a specialty wipe for male connectors and a swab for female connectors.
For the most effective cleaning, it’s important to know which fiber-cleaning tool to use. Mechanical clicker-style tools are quick and good for applications with light levels of contamination. They can help fabricators efficiently clean a high volume of connectors.
Because cleaning sticks make full contact with the end-face configuration, they clean the entire area without the need to disassemble the connector or adapter. They often give the largest effective cleaning region on the entire surface, eliminating persistent problems associated with contaminants migrating into the light signal path.
A cleaning stick should be engineered specifically to match the configuration and size of the end-face and be non-linting for optimal cleaning. When using the stick, it is important to only rotate in one direction; typically, six rotations in one direction is enough to remove any contamination. Use only one stick per end-face to avoid cross-contamination.
If using a wipe instead of a cleaning tool or stick when cleaning fiber end-faces, insist on high-grade wipes that do not produce lint or generate a static charge. Optical-grade wipes are strong, soft, and won’t scratch delicate ceramic or composite end-faces. They are also highly absorbent to completely wipe away contamination without leaving residue or lint behind. It is important to ensure the wipes you use come in sealed packages—this helps keep them pure and clean prior to use.
Proper end-face cleaning is an important step to ensure consistent and reliable PCB performance. Use specially engineered fiber-optic cleaning products and adopt the recommended three-step ICI cleaning process for all end-faces before connecting. These simple steps can keep the PCB operating as intended and without fault.
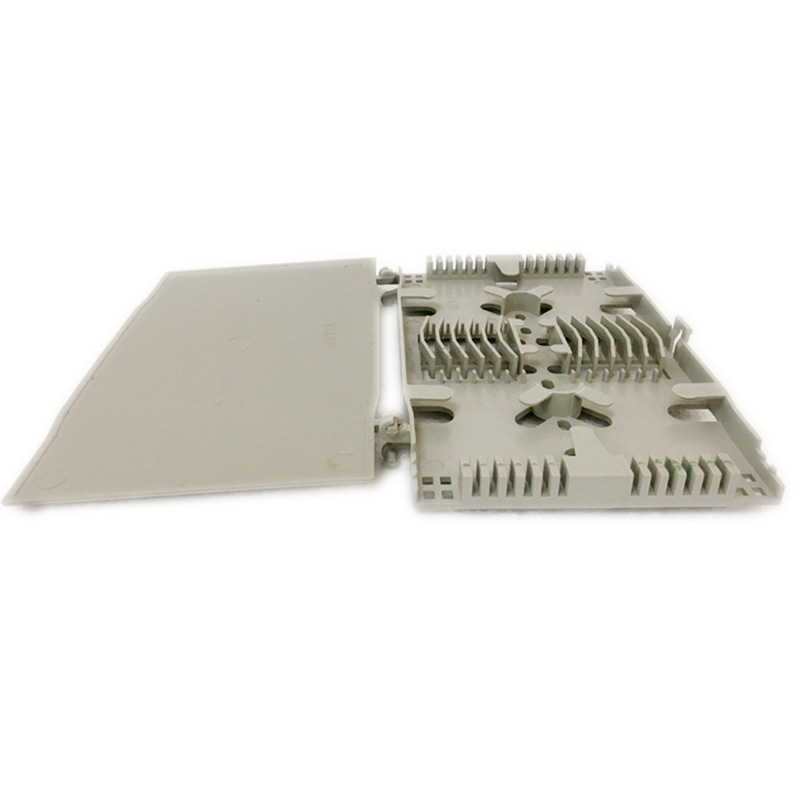
Protection Sleeve Fiber Optic Liam Taylor is European business manager, fiber optics at MicroCare U.K. Ltd. (Leeds, U.K.) and a member of IEC/SC 86B Working Group 4.