5-Axis Multi-sensor Vision. Image Source: Renishaw
In the world of manufacturing, precision is paramount. The ability to accurately inspect components is crucial to ensuring quality, reliability, and efficiency. Having a traceable reference of physical dimensions at each manufacturing plant ensures the interoperability of components produced globally. This is where coordinate measurement machines (CMMs) play a vital role. CMMs have revolutionized the manufacturing industry by providing highly accurate and traceable measurement capabilities. In this article, we will explore the use of CMMs, advancements in technology, and their growing contribution to support leading developments in automation, artificial intelligence, and machine learning. Optical Measuring System

Coordinate measurement machines are sophisticated devices used to measure the physical geometrical characteristics of an object. They utilize a combination of probing hardware, programming and analysis software, and precise positioning systems to capture data points on an object’s surface, allowing for dimensional analysis and inspection. CMMs can measure intricate features such as holes, curves, and complex geometries with high precision. The CMM provides traceable measurement through certification via performance assessment standards like ASME B89.4 and ISO10360-2, which will result in a statement of the maximum error expected over a given length of measurement.
A. Frame: The structure of a CMM that provides fundamental positioning is typically referred to as the frame. The frame provides the movement of a probing system in XYZ coordinate system. Each axis typically rides on an air bearing and is driven using an electric motor (rotary or linear) and provides positioning feedback using a scale/encoder that can resolve to a fraction of a micron. The primary type of frames includes cantilever, bridge, gantry, and horizontal arm, with bridge being the most common. Frames are typically labelled showing the volume of the measuring area in 100mm increments. A 12.12.9 CMM would have a measurable range of 1200mm in X, 1200mm in Y and 900mm in Z.
B. Probing Systems: The probing system provides the actual point collection on the surface of the part being inspected. Modern CMM measurement was made possible by the invention of the touch probe by David McMurtry while at Rolls-Royce Aerospace in the 1970s. Today, there are a range of probing system technologies available to suit applications. Scanning probes, both contact and noncontact, allow for the collection of high-density surface data at rates of thousands of points per second. In some cases, additional positioning axis are employed in a “probe head” that can position the probe relative to the part and the frame. Probe heads also provide quick couplings to facilitate automatic exchange of probing technologies. This multi-sensor CMM capability allows for several types of measurements to occur on the same frame, reducing floorspace and manpower requirements in modern factories.
C. Programing and Analysis Software: Software is required to operate and obtain data from modern CMMs. OEM manufacturers of CMMs typically provide software to operate their machines. In addition, there are a growing number of software platforms that can be used across multiple brands of CMMs. These have the capability to run various makes and models of CMMs.
A. Open Architecture Design: Led by the National Institute of Standards and Technology (NIST), a specification called I++DME has been developed that is supported by leading CMM manufacturers globally. CMMs manufactured to the I++DME specification offer interoperability with a wide array of software platforms available now and offer “future proofing” of systems to support software that has yet to be developed.
B. Multi-sensor Capability: New sensor technologies are being introduced that further increase the flexibility of CMMs. These include Vision (camera), Structured Light (fringe), Ultrasonic Thickness and Temperature. The measurements benefit from using a common part reference datum that reduces correlation errors (a traditional problem when using multiple devices to measure). Also, by facilitating multiple measurements on a single device, floor space is minimized, inspection throughput is increased, and manpower requirements are reduced.
C. 5-Axis Positioning and Measurement: Advances in probing head design have made full 5-Axis measurement possible. 5-Axis systems utilize high precision rotary motion and encoder feedback that when used in combination with machine frame positioning, significantly increase inspection speed by as much as 50X over traditional 3-Axis frame positioning only. This is especially valuable when measuring non-prismatic features such as aerospace blades/vanes and cylindrical features such as bearings and bores. Throughput is further enhanced by 5-Axis systems being able to adapt to changing part orientation, making the systems capable of supporting autonomous learning systems.
D. Shop Floor Integration: No longer used in laboratory only, shop floor hardened CMMs are being produced that can be used in wider temperature ranges (40 degrees of change can be handled now versus 1-2 degrees required for traditional laboratory grade systems) and can be more easily integrated into automated manufacturing lines and robotic systems. Enclosures with power and air filtering and conditioning, and pallet-based transfer systems with flexible fixturing are readily supplied by leading CMM manufacturers. The use of automated shop floor systems enables seamless measurement, inspection, and process feedback loops, leading to improved productivity and reduced human error.
CMMs find application in a wide range of industries, including aerospace, automotive, medical, and consumer goods. For example, in aerospace manufacturing, CMMs are used to measure complex airfoil shapes and critical engine components. In the automotive industry, CMMs have long been employed to inspect the precision and tolerances of engine blocks, transmission components, and body panels, but are also leading the way with inspection of the new hybrid and full battery electric powered systems being deployed.
In the medical industry, CMMs are used to validate final part acceptance especially where devices are to be implanted in the body, when 100% part inspection is required to meet FDA approval. Increasingly, measurements are taken during individual stages of the manufacturing process to control variation at the source so that manufactured costs can be kept low for consumers.
Surprisingly, the needs of both consumer electronics and defense systems require rapid inspection of new design concepts developed to “stay ahead of the competition.” This is an area where CMM technology is crucial as it allows for very flexible measurement that can be easily programmed for novel geometries explored when developing the next new product.
A. Integration with CAD/CAM/PLM software: As the manufacturing industry matures, we are seeing companies seek to reduce the number of different software packages that are required to support operations. Software solutions that offer design, manufacturing and inspection in a single platform are being sought to replace individual packages. Further use of embedded product manufacturing information (PMI) in 3D models could drive even more reduction in software variants being used.
B. Artificial Intelligence: The measurement data provided by CMMs powers artificial intelligence and machine learning algorithms being developed in the manufacturing industry. Real-world metrology reference is required to unlock the value of analyzing complex data patterns.
C. Digital Twin Technology: CMMs play a vital role in the development of digital twins, virtual replicas of physical objects or processes. By capturing accurate measurements and comparing them to digital models, CMMs can provide the fundamental accuracy of digital twin simulations.
Coordinate measurement machines have become indispensable tools in the manufacturing industry, driving precision, quality, and efficiency. Through advancements in technology and developments in measurement methods, CMMs continue to contribute significantly to many industrial sectors. As CMM technology continues to advance, we can expect further improvements in accuracy, speed, and integration, further transforming the landscape of modern manufacturing.
Dan Skulan is the General Manager of Industrial Metrology for Renishaw Inc.
You must have JavaScript enabled to enjoy a limited number of articles over the next 30 days.
Sponsored Content is a special paid section where industry companies provide high quality, objective, non-commercial content around topics of interest to the Quality audience. All Sponsored Content is supplied by the advertising company and any opinions expressed in this article are those of the author and not necessarily reflect the views of Quality or its parent company, BNP Media. Interested in participating in our Sponsored Content section? Contact your local rep!
On Demand Join this webinar to learn how companies of all sizes are adopting easy-to-use cobots to overcome the labor shortage, handle multi-shift operations, scale production on-the-fly, and solve many other challenges.
In today’s rapidly evolving industrial landscape, the key to staying competitive lies in embracing modern technologies and a lean manufacturing mindset.
Copyright ©2024. All Rights Reserved BNP Media.
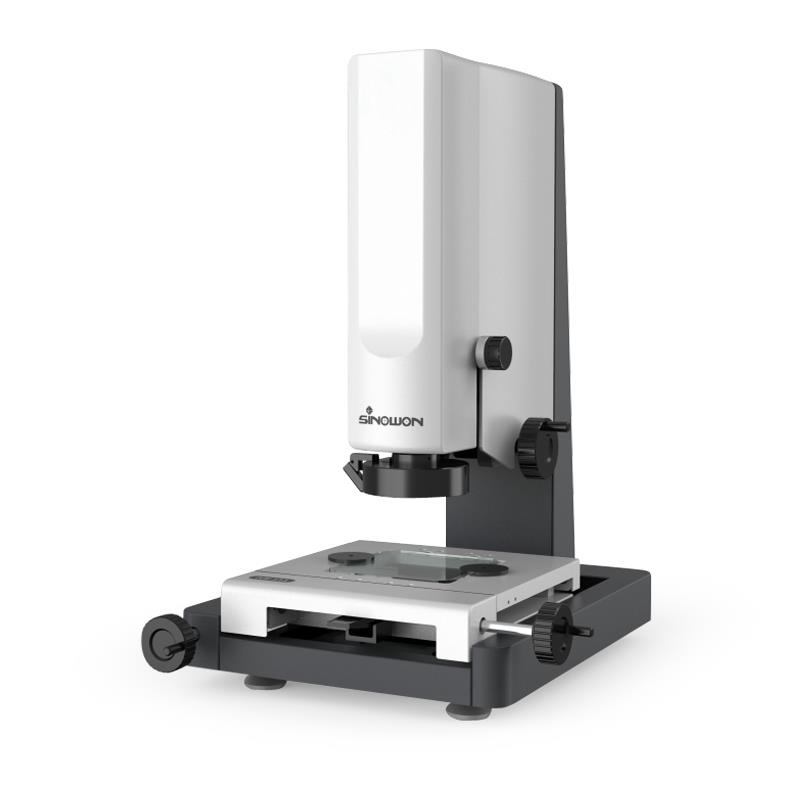
Automatic Inspection Machine Design, CMS, Hosting & Web Development :: ePublishing