Depending on the chef’s skill, many exciting things can happen in the kitchen. Few, however, grab as much immediate attention as when a piece of foil or a fork accidentally (?) makes it into the microwave oven. That usually makes for a dramatic light show, accompanied by admonishment about being foolish enough to let metal anywhere near the appliance. So what’s the deal with this metal-melting microwave?
As it turns out, with the proper accessories, a standard microwave makes a dandy forge. Within limits, anyway. According to [Denny], who appears to have spent a lot of time optimizing his process, the key is not so much the microwave itself, but the crucible and its heat-retaining chamber. The latter is made from layers of ceramic insulating blanket material, of the type used to line kilns and furnaces. Wrapped around a 3D printed form and held together with many layers of Kapton tape, the ceramic is carefully shaped and given a surface finish of kiln wash. High Purity Carbon Graphite Crucible
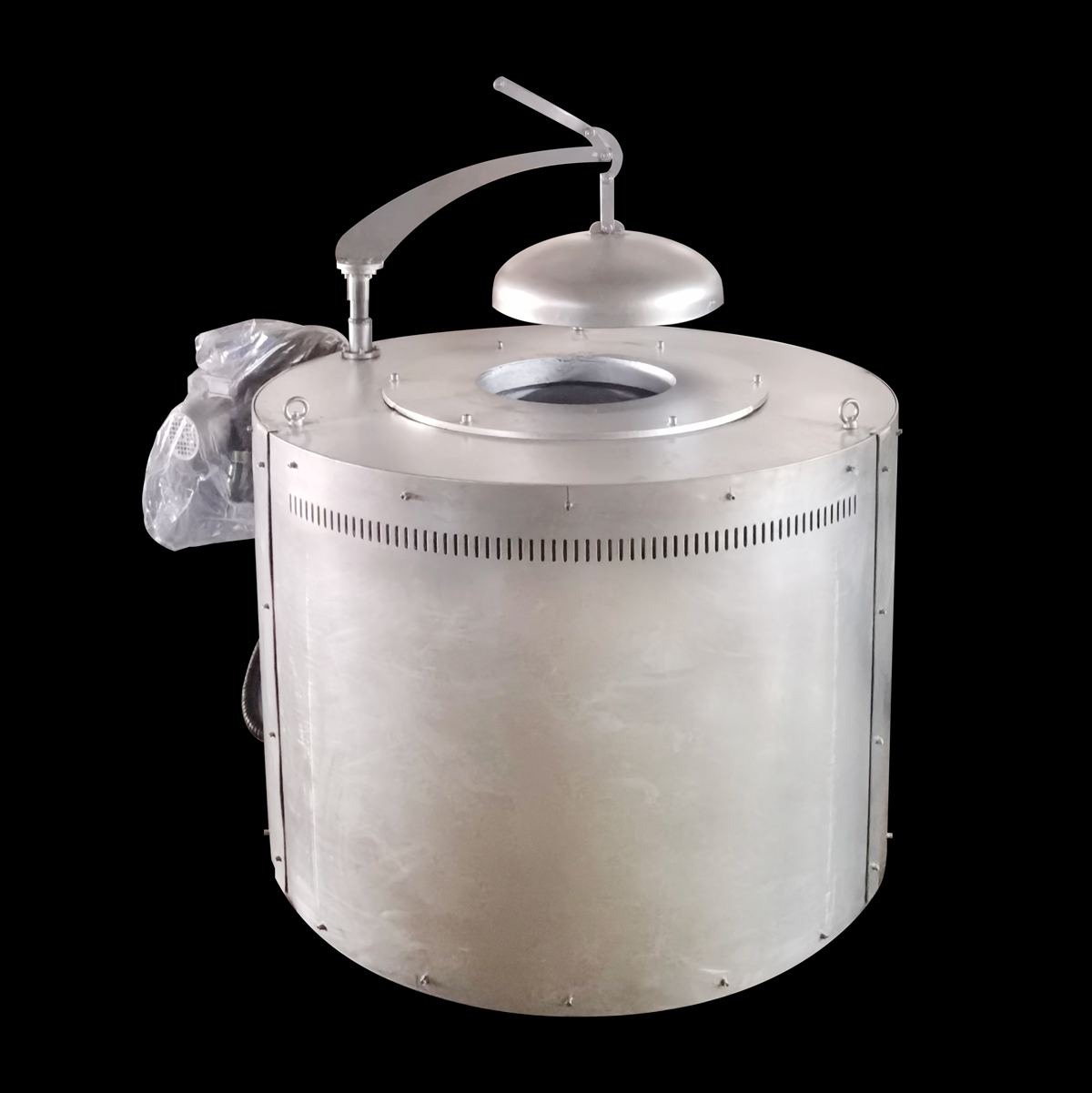
While the ceramic chamber’s job is to hold in heat, the crucible is really the business end of the forge. Made of silicon carbide, the crucible absorbs the microwave energy and transduces it into radiant heat — and a lot of it. [Denny] shares several methods of mixing silicon carbide grit with sodium silicate solution, also known as water glass, as well as a couple of ways of forming the crucible, including some clever printed molds.
As for results, [Denny] has tried melting all the usual home forge metals, like aluminum and copper. He has also done brass, stainless steel, and even cast iron, albeit in small quantities. His setup is somewhat complicated — certainly more complex than the usual propane-powered forge we’ve seen plenty of examples of — but it may be more suitable for people with limited access to a space suitable for lighting up a more traditional forge. We’re not sure we’d do it in the kitchen, but it’s still a nice skill to keep in mind.
I think the main issue is that the max power of a standard microwave. I just checked online some commercial consumer propane forges, and they claim to go up to 50kW.
Meanwhile, a microwave will only go up to 1kW, which makes it not a real contender against them.
However, I like this idea, and I have already seen it used to make ruby (using a small crucible), and to melt glass.
Propane forges take quite a lot longer to heat up, because of their much larger thermal mass, and while I’m not arguing this is a good qualification, his setup is clearly possible to do inside while a propane forge really isn’t. At least mine isn’t. The room would be exceptionally warm and full of carbon monoxide/dioxide after the 25 minutes it takes to get to casting heat. On the other hand, my foundry can do 20kg of aluminum. You couldn’t even fit my crucible in that microwave.
Not to mention that the vast majority of the 1kw is going into the crucible whereas a propane forge loses a lot of heat in exhaust.
Plus this seems far more useful for quick small scale projects, maybe jewelery or small replacement parts. Wouldn’t want to melt down a year’s worth of cans with this thing.
If a little physics and math are used (I know, old school, too complicated for this bunch),you’ll find this
Aluminum has a heat of fusion of 321 Joules/gram. Converting lbs to grams, 50 lbs = 22679 grams. So the total heat required in Joules (watt-seconds) is 22,679 * 321 = 7,279,959 watt-seconds. Converting to watt-hours, 7,279,959 / 3600 = 2,022 watt-hours. Converting to BTU, 6899 BTU/hr. To do the melt in 45 minutes, 6899 / 0.75 = 9198 BTU/hr.
A 50 kW propane burner produces 170,607 BTU/hr. 170,607 * 0.75 = 127,955 BTU per 45 minutes. The efficiency is 9198 / 127,995 = 7.2%.
So about 7% of the heat of combustion transfers to melt the aluminum in 45 minutes.
The meter-to-metal efficiency for induction process is around 80%. I’ve never tried microwave but I know that the magnetron is only about 60% efficient so the microwave would use a little more energy but at nowhere near the cost of a propane burner.
Propane’s heat of combustion is 21,640 BTU per pound. I returned from a trip yesterday and noticed that the tank exchanges at C-stores in this area are charging $35 for 15 lbs in a 20 lb cylinder. That 35/15 = $2.33 per pound. To produce 127,995 BTU per 45 minutes requires 127,995 / 21,640 = 5.9 lbs of propane. At $2.33 per pounds, that’s $13.78 for the run.
I pay 0.12 cents/kWh here. 7kW * .75 = 5.25 kWhr. 5.25 kWhr * $0.12 = $0.68 for an induction run.
If you want to see a demonstration run of melting aluminum in my kitchen, go here:
https://www.youtube.com/watch?v=o–6HH8Nxgg
The Roy induction heater is our 1500-2000 watt version. I call this my Kentucky Fried Furnace because I made the crucible assembly using a KFC bucket as the mold. We did it just because we could :-) Obviously I wasn’t married then!
My induction furnace that uses a Kanthal heating element used to use 1.4kwh (now 3khw afer rewinding lazily) and manages to melt a good size graphite crucible, 3kg. I’ll be doing the microwave mod next, looks much more efficient to me, and I think if I can find a big enough microwave, I’ll be able to use the stack of silicone carbide crucibles I’ve got I kept meaning to use with the bigger elelctric furnace i’m 3/4 of the way building and left to get cobwebby lol
NO a Kanthal heating element is a RESISTIVE Heater. Little wire gets hot when electrons are pumped through. an induction heater uses a coil to INDUCE current in the workpiece causing it to get hot as electrons are motivated by the coils magnetic field. If you have Kanthal heating elements you do NOT HAVE AN INDUCTION HEATER. Get one. They work and are far more practical than microwave.
LOL my bad, been too busy drooling over induction furnaces the past few weeks to get things right way around, I know the mistake i made, thanks for dumbing it down for the rest of the world :D
Totally Wrong! I’m the Chief Engineer for Fluxeon.com, a company that sells induction heaters including light metal melting. I design all our products. I use heavy gauge Kanthal as the work coil so it can be positioned in the heat zone for better coupling to the crucible. It has an approximately zero thermal coefficient of conductivity so my heater does not have to compensate as the work coil heats up. We build-to-order a 50 lb aluminum furnace that melts the aluminum in about 20 minutes using 7kW of induction power.
I will design to a silicon carbide or induction-ready graphite (plain graphite crucibles barely induction heat. Induction-ready graphite crucibles contain a magnetic additive, probably magnetite, to make them more susceptible to induction.) crucible but I much prefer a cast iron crucible. We use a barrier coating on the inside, designed to prevent iron getting into the melt when using cast iron pots.
1Kw of nicely focused on an insulated vessel is quite a lot of heating energy
Microwave heating is direct though, propane blasts a lot of hot gas around the place and a hell of a lot of heat escapes with the exhaust.
1kW pumped directly into something is pretty effective, kinda like how microwaves are faster & more efficient than traditional stove tops.
1 Kw is plenty for small projects. I have a small resisitively heated hobby kiln that plugs into 110VAC and is quite capable of melting metals. The microwave hack looks even better because more of the energy gets focused into the crucible instead of heating the body of the kiln.
A forge gets metals hot enough to bash them into shape.
A foundry gets metals hot enough to pour them into shape.
Seeing as we are nitpicking, this is a furnace…
A foundry is a place or facility where metal is melted and poured into shape.
A furnace is a device or structure that gets metal hot enough to pour into shape.
I thought it was a hearth…
Actually, actually, a furnace is a structure in which heat is produced. It isn’t necessarily related to making metal liquid. Foundry has several meanings and is appropriate in this case.
Remember, if you do this, use a dedicated microwave and not one that is used for cooking foods. If you do then invariably you will end up eating bits of melted metal. Nothing good will come from that.
I’d argue some food-stuff you can microwave is at least as bad for your health. Btw.: eating chunks of metal like steel, copper, tin, won’t do you much harm at all..
copper and tin definitely will
Not a Goldschläger fan?
You just unlocked a lot of rather bad college memories I had happily repressed. Took me a while to get to where I could eat cinnamon toast again.
If it’s melted, it would be mercury or caesium or gallium. Yummy!
seems like you’d be losing a lot of energy in the transformer and magnetron and direct element heating would be more efficient.
heh i started thinking about this and then you’d get a different kind of loss, if i understand correctly. if you put the heating element on the outside of the ceramic chamber, then you have to pump the heat through that barrier (with it escaping outside the whole time). or if you put the heating element inside of it, or even inside of the crucible, then the heating element itself would be in a pretty hostile environment. i don’t know, is it possible to get a cheap common heating element that can survive that duty?
my point is that my kind of naive assumption i bring that direct resistive heating is trivial might go on its head at temperatures this high because the heating element must reach a higher temperature than the target material. but the microwave emitter is physically isolated and doesn’t have to reach any particular temperature. maybe the advantage isn’t efficiency but rather some sort of ‘plausibility’ or ‘durability’ factor.
Good video, lots of hard earned knowledge given, injecting Co2 into sodium silicate hardens it instantly, but the crucible would probably still need the heat treatment. Genuine question for Hackaday readers, why are heating boilers not microwave powered?.
Because heating resistively is 100% efficient use of the electricity where microwave ovens have lots of loses via the transformer and magnetron.
Many boilers are also powered by gas or oil not electricity.
I anticipated this answer, because it is true, but immersion heaters are usually in a metal tube with electrical insulating powder, this must reduce efficiency and add latency, I can not envisage a 1KW element heater melting metal in four minutes. Many boilers are powered by gas or oil, but air and ground source heat pumps are being pushed as the only alternative in the UK.
Reduces effectiveness, but with immersion heaters it’s fairly reasonable to assume that very little heat leaves the device without entering the water first, and that the energy of heating the thermal mass of the device is much less than that of heating all the water. So efficiency is still approaching 100% in simple estimation.
Fun fact- someone has actually tried this. https://www.theguardian.com/environment/2021/mar/16/first-microwave-powered-home-boiler-could-help-cut-emissions
How about an induction heater, if you want to heat up some steely stuff?
Induction heaters take a *lot* of power; for a similar metal-melting capacity, you’d need around 10-15 kW. (This is because crucibles, bars of steel etc don’t couple to the coil as well as a proper transformer would.) Microwaves on the other hand do a very good job of making sure that pretty much all energy added into the chamber eventually gets absorbed by the target.
This is not a forge, it’s a furnace. Forges heat metal below its melting point, usually for blacksmithing, and have an opening so that parts can be inserted or withdrawn quickly.
I will stick with coal for now,and upgrade to charcoal once I get a retort built on a scale that will also produce extra for soil amendment and carbon capture have no problem melting iron ,aluminum and bronze in fact the limitation isnt melting iron,its not burning it which is fun,but not the point
Melting metal in a microwave, yep, that’s a hack.
We used induction heaters for our molybdenum and tungsten crucibles to melt aluminum oxide to grow sapphire parts. The frequency was 9600 Hz, just below FCC regulations for RF radiation. We needed much higher temperatures, about 2200 C. At those temperatures, we needed to exclude any oxygen that would cause those crucibles and insulations to burn up. Our chosen gas was argon. We first pulled a vacuum on the system to draw oxygen out of the parts and then backflushed with argon. For a 2″ crucible for growing fiber, power was 25 KW. Our big systems were 250 KW for slabs 3/8″ thick, 12″ wide and about 15″ long. I’m sure they are doing much larger pieces now. The chambers were either double wall pyrex or quartz or double wall stainless steel cooled with deionized water. The parts were glowing like a light bulb so we used 2 color pyrometers for PID control. We could control to about 1 degree. Growing sapphire crystals to accurate size is fussy. I use a microwave now to dry green turned wood in a vacuum chamber. The microwave heats the water in wood very nicely. A process that normally takes 6 months to a year is reduced now to about 50 minutes. I monitor the weight loss with a load cell so can easily plot the change in weight. Power applied is moderated in the usual way with duty cycle changes. Just observations that are mostly on topic.
I’d love to see a writeup of that process to dry wood in the microwave!
Me too about the write-up. Trying to picture a vacuum and a load cell in a microwave. I imagine the pieces of wood you’re drying are small.
Maybe it’s not “in”, Earle just defeats the door switch and points the microwave at the bell jar.
I would love much much more detail on the sapphire crystal furnace. There is very little practical information for the physical characteristics on induction furnaces. Have a very unique need not commercially filled, and not relating to jewelry, for a Czochralski sapphire furnace to do small sizes of sapphire with certain properties. Been investigating if it is feasible to run at home. Do you have a website?
Making khyber cystals you must … young padawon
I’ve seen magnetrons used industrially where the unit is basically just a big metal box with multiple magnetrons along the side of it. Makes you wonder how big you could make one of these metal melters, and how efficient they could be if you used aerogel for insulation.
That was my immediate thought, what would multiple magnetrons in a single unit do? Can they be directly opposed to one another at 180 degrees, or would you need an offset? Would you need to worry about microwave interference between units? Could you produce better results with resonance between multiple magnetrons?
I need someone with more time and money on their hands to figure this out.
How about…. 1 metal (possibly fluid cooled) parabolic reflector of sufficient diameter a polar array of 4-8-120? magnatrons a spherical metal (possibly fluid cooled) chamber with an opening matched to the focal cone of the primary reflector
I recall one image of such a build where they were simply in a row along the side of the box, may have been a continuous production set up so “stuff” was passing along in front of each in turn.
This has been being done in university engineering labs since about the mid 90s – it seems to work fairly well.
Do yourself a favor and .. don’t dry brush ceramic fiber off surfaces. Ceramic fiber dust is nasty. Work outdoors, wear a respirator, and do the scrubbing step with water and a surfactant (dish soap, shower gel,…). Don’t use a non-HEPA vacuum for clean-up.
CAS #: 142844-00-6 CERAMIC FIBRES (ALUMINOSILICATE) https://www.ilo.org/dyn/icsc/showcard.display?p_card_id=0123&p_version=2&p_lang=en
Please be kind and respectful to help make the comments section excellent. (Comment Policy)
This site uses Akismet to reduce spam. Learn how your comment data is processed.
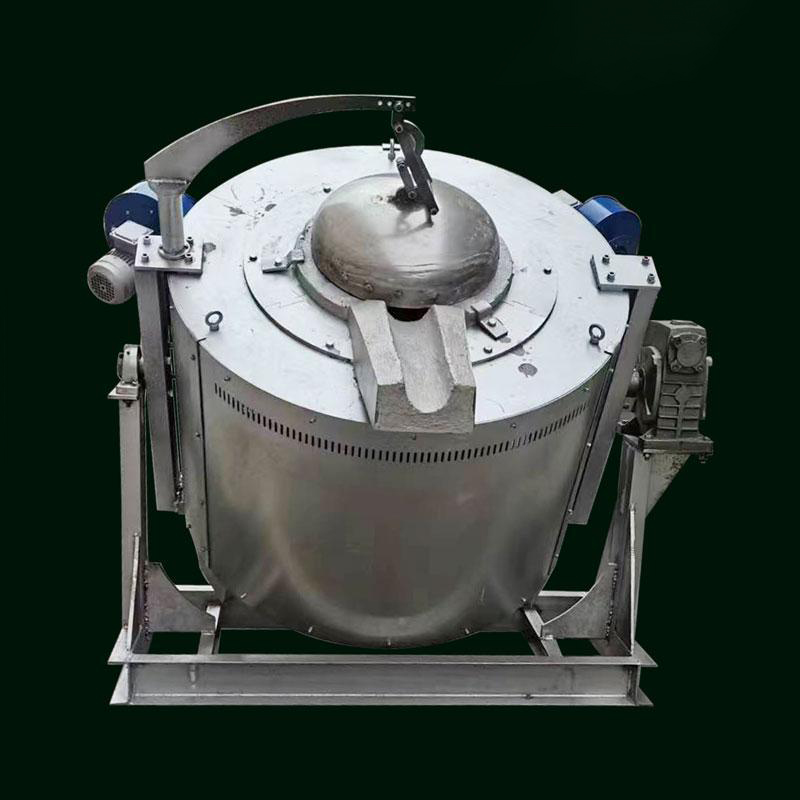
Clay Bonded Graphite Crucibles By using our website and services, you expressly agree to the placement of our performance, functionality and advertising cookies. Learn more