After nearly four decades at Hytrol, chief engineer Boyce Bonham has a good perspective on the latest trends in conveyors and sorters. He sums it up this way: “The big push today is to get more output from the same building footprint.”
Sounds simple enough, but satisfying that need requires some innovation. That ranges from systems able to handle a wider range of product at high speed without interruption. Intelligent Sorting

In short, versatility and speed are key words for conveyors and sorters in early 2023. And little wonder. E-commerce continues to increase operational demands as DCs handle packages ranging from polybags that weigh a few ounces to extremely large cartons previously thought to be non-conveyable.
Steve Miskelley, vice president of sales for MHS Conveyor, calls it an “expansion to the extremes. We’re all focused on broadening the spectrum of what a single system can handle.”
The result, says Bonham, is items not previously thought of as conveyable or sortable are now. Examples are furniture and other items weighing 200 to 300 pounds, he adds.
At the same time, autonomous mobile robots (AMRs) are moving into the mix of materials handling equipment fulfilling orders of all types. And while AMRs are hardly a dominant technology today, barely a single conversation about distribution center operations goes by without at least a passing mention of them.
Quite simply, the DC landscape facing conveyors and sorters is quite different than what it was a short time ago. And by all accounts, it will continue to change for the foreseeable future.
If you listen casually to equipment conversations these days, AMRs are the answer to everything. After all, they are highly mobile and aren’t bolted to the floor, eliminating traffic obstacles. They make their own decisions and are operationally very flexible. Also, AMRs are much easier to install than conveyors and sorters. What’s not to love?
Well, Dennis Schuitema, Dematic’s product manager for conveyor and sortation, offers a few counterpoints.
To begin, AMR systems currently are not capable of hourly throughput of 18,000 to 20,000 cases an hour in a similar footprint as conveyors and sorters.
Furthermore, loading and unloading AMRs is currently either a manual operation or a relatively slow automated process. Both conveyors and sorters are capable of induction and end transfer of hundreds of cartons a minute.
And while AMRs are not fixed path equipment, they are very definitely part of the floor traffic of a facility.
“In reality, conveyors, sorters and AMRs are complementary. But it does take time to understand how the technologies can work together in a given facility,” says Schuitema. In other words, we are nowhere near the cookie-cutter stage here, but there are benefits to combining the three technologies.
Honeywell Intelligrated’s specialist for conveyors and sorters, Rui Cai, says “by adding robotics, end users can achieve a more advanced take on integrated systems. The result is a significant reduction in the cost of the solution, system footprint and labor requirements, while optimizing the flow of packages.”
Or as Bonham said earlier, it’s all about getting more output from the same building footprint.
And while there might be a lull right now in demand for this equipment precipitated by Amazon’s pullback on many new projects, conveyors and sorters remain a stalwart, and with good reason(s).
Perhaps only slightly tongue in cheek, Schuitema says “people know what to do around conveyors.” They are a known quantity. He also cites their reliability and simplicity as what people like about them.
The idea for suppliers now is to give users more to like. Time and again, they talk about more versatile systems. Versatility comes in different forms.
One is more modular conveyor and sortation systems, says Interroll’s Barry Miller, vice president of sales and service. “It’s all about being able to install, maintain and reconfigure conveyor and sortation systems as needed,” he explains.
“The majority of users want modularity now. We have seen a major increase in that request in the past two years,” Miller says. “Modularity allows them to reconfigure their systems as their business, product and volumes change.”
He talks about Interroll’s modular conveyor platform (MCP) that allows sections of conveyor to be set up one day and reoriented over time as needed for product and volume shifts. Multi-control cards that communicate with each other across different sections of conveyor also figure in the modularity equation. “The cards can just be plugged into the conveyor as needed to provide localized control,” says Miller.
And those volume and product shifts seem to be in perpetual motion now. Over at MHS Conveyor, there’s a focus on flexible zones capable of handling on the fly a change in package size, says Miskelley. “For instance, one package might need two zones of space on the conveyor while the next one only needs one zone.” He notes this is especially valuable in e-commerce as the volume and diversity of polybags continues to increase.
Higher speed is also critical here, says Miskelley. “Systems need to be able to feed it, take it away at high speeds with a good bar code read the first time through,” he adds.
Honeywell’s Cai says there is a growing emphasis on improving bar code read rates and eliminating mis-sorts. “We have not only been developing and applying advanced computer vision and artificial intelligence technologies here. Utilizing the latest cost-effective package detection and product orientation capturing technologies helps to increase the bar code read rate,” says Cai.
He continues to talk about a full-width belt cartridge for motor driven roller (MDR) conveyors. The cartridge can be swapped into/out of the system in less than a minute, he says, allowing the same system to handle polybags and totes with equal ease.
In discussions with suppliers, new variations on shoe sorters and narrow belt sorters came up repeatedly. With the former, the emphasis from Honeywell is on flexibility for divert/lane placement. And with the latter, MHS Conveyor focuses on the versatility of handling everything from small cartons to much larger items that are awkward to convey.
But perhaps the most off beat sorter is the pouch sorter. The fact that pouch sorters exist at all is a testament to the versatility of sortation equipment in general.
These systems are a series of pouches hung from the ceiling where single items are buffered, sorted and sequenced, explains Terry Brown, sales director for logistic systems group at Beumer Group. They handle more than 10,000 items an hour, saving floor space while minimizing manual touches. Pouch systems also serve as a goods-to-person system for final picking. They are most widely used in the apparel industry.
While not everyone thinks of the quality of life in a DC, there is such a thing. And with sorters and conveyors, it usually comes down to sustainability and noise.
You can’t underestimate the value of energy efficiency and sustainability, says Jordan Mukite, key market specialist for intralogistics at NORD. Variable frequency drives (VFDs) figure prominently with sorters and conveyors.
VFDs adjust the voltage to the motor and control the speed, increasing efficiency and managing demand for electricity, says Mukite. As a result, VFD offers an improved ability to match the conveyor or sorter speed to the specific product being handled at the time.
In fact, energy efficiency goes beyond VFDs, says Mukite. “There is a desire by operations managers to focus on potential energy savings right now. Not only are they looking to trim their own electrical demand, but they want conveyors and sorters that run more efficiently.
For some time now in the push to greater sustainability, IE3 rated motors have been the baseline. But now, users are starting to ask for IE4 and IE5 rated motors. Which is an interesting twist, says Dematic’s Schuitema. The IE4 standard is in place, but “the IE5 standard has not been officially released. It’s just well known what the standard will be,” he adds.
Noise reduction with sorters and conveyors is a tricky proposition. While the materials handling equipment certainly contributes to noise levels in the facility, so does whatever is being moved. Totes in particular act like a big bass drum.
In any case, the typical noise levels for these systems are in the low 80 decibel range. The objective is to get that to the mid-70s. For point of comparison, an office area is usually in the low 70s to high 60s. Use of belts rather than rollers typically goes a long way to turning down the noise.
At this point, it’s reasonable to assume preventative maintenance is the baseline for conveyor and sorter systems. After all, if either goes down unexpectedly it can have a major impact on the day’s throughput.
Now, predictive maintenance programs based on saved and real-time data are beginning to emerge. Most operations are at the early stage of collecting the data. This is typically done by sensors mounted near key moving parts to predict extra wear or increased temperatures that indicate a potential failure. Vibration sensors are part of the mix, too.
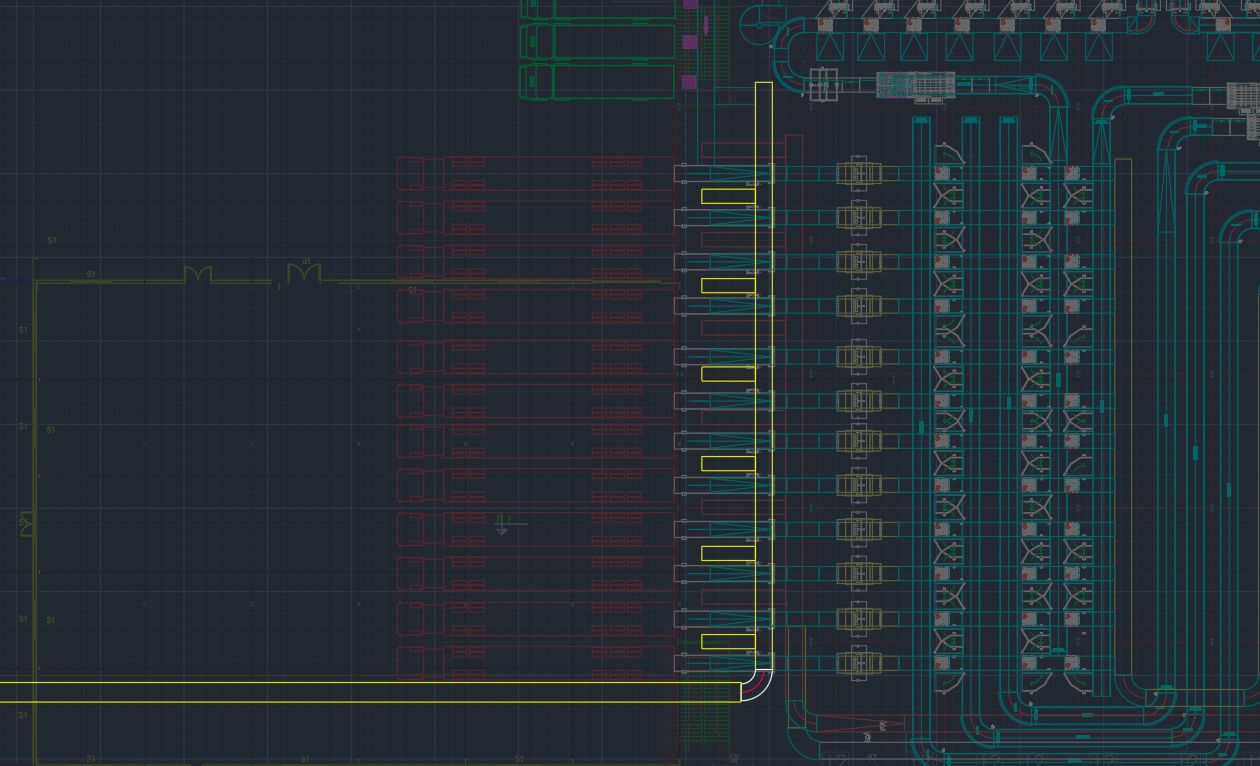
Ring Cross Belt Sorter In addition, some suppliers offer programs that collect the data, monitor equipment status and predict potential failures with the help of advanced analytics. While this may be in the early stages, predictive maintenance is clearly the future for keeping systems up and running.