As machine shops add new CNC machine tools, they have to rethink how the new equipment will fit in with existing component production processes. Sometimes this will require the shop to re-programme the machining process, invest in different cutting tools, or create new fixturing. It can also call for a shop to make bigger-picture changes. As Wekaba Precision Engineering, a manufacturer based in Alrode South, Gauteng, recently experienced, this process can be challenging, especially when it comes in the middle of the pandemic and a drastic increase in orders for components. But by drawing on past experiences and rethinking some aspects of their production process, the shop is now more productive and successful.
“Process and equipment modernisation is scary but necessary. When done correctly, both can help secure a shop’s future in the industry and open new opportunities. Admittedly, we had fallen a bit behind with our machinery investments. It’s no excuse but when you already have over 100 CNC machines in the factory turning out hundreds of quality components then you do hold back on investment. However, we have now undergone an innovative development period in the company that includes capital equipment purchases and a building construction and renovation to house the new machines,” explained Wekaba business development manager Neil Sewnarain. Precision Components Inc

Wekaba focuses on manufacturing customer specific, machined components, specifically turned and milled components, and can produce upwards of 10 million components per annum
“Wekaba’s establishment goes back to 1981 when two brothers with German heritage – Werner and Klaus Baller – decided to open a precision engineering company to service the mining industry. Their initial focus was to produce hydraulic products and components and they are still the mainstay of the company 42 years later. From humble beginnings of having the use of three conventional machine tools and employing two staff the company has grown to such an extent that it now employs 485 staff and operates on a two-shift system.”
“We are regarded as experts in the field of repetitive, medium to high-volume machining but the company is not just about that. Mining products and components have had strong influence over the years and in particular a bias towards hydraulics. Currently mining related products and components makes up 75% of the product mix when it used to be 100%. This reduction in the percentage on the mining side is not because we have lost business. It is in fact the exact opposite and we continue to see growth on this side.”
Wekaba has recently invested in 15 new DN Solutions CNC turn mills
“We now have the capacity to consistently produce various suspension components at volume for 1st and 2nd tier automotive suppliers and we also manufacture CNC turned and milled components for other industries including automotive, rail, construction and industrial hydraulic componentry. The automotive and rail transport industries roughly account for about 10% each of our production capacity and the general industry accounts for the remainder.”
Adapters, wedges, hose fittings and modulars “Our manufacturing facility can accommodate orders from one to several 100 000 components with capabilities that include CNC turning, CNC milling, CNC tube-bending, copper fusion brazing and annealing, finite element analysis and more. These diverse capabilities allow us to manufacture specialised components in various geometries and using all technologies whether custom or standard.”
Sewnarain highlights: “Wekaba is one of the top manufacturers in South Africa of one-piece 90º and 45º stainless steel fittings and produces a range of hose fittings and collars, with applications in industrial sectors. Wekaba’s BSP female welds on fittings for use on metal-braided hoses are also used in industrial areas.”
“We decided to go the one supplier route and of the 17 new CNC machines we purchased to house in the new building, 15 of them are DN Solutions’ turn/mill machines that have been supplied by Puma Machine Tools. They are made up of the Puma GT 2100 and Puma DNT 2100 ranges and most of them have been supplied with an Iemca Advantage series bar-feeder. This gives you some idea of the type of work they will be doing.”
“Our hose fittings and collars include straight fittings and elbows, 1 and 2 wire and multi spiral tails, flanges and threads to suite -04 to -32, skive, non-skive, 1 and 2 wire and multi spiral collars. All are manufactured in mild steel or stainless steel.”
“Our modular adapter system allows for straights, elbows, T and cross piece configurations with NPT, BSP, ORFS, ORB, JIC, metric or staple lock ends from -04 to -32. These products are manufactured in mild steel and are zinc plated.” “Our post tension and re-stressable anchor heads are manufactured to customer requirement with various options and configurations.”
“Our wedges, which are used in the mining and tensioning market where 100% reliability is the benchmark, locks steel strand in the conical hole of the wedge block. Wedges are pieces of tapered high-strength heat-treated steel with internal serrations (teeth) that penetrate the prestressing steel during transfer of prestressing force.”
“The anchorage systems wedges and barrels are also used in pre- and post-tension concrete manufacturing.”
A general view of the new building where the DN Solutions machines are housed
“We also have expertise in the manufacture of made to order ranges specific to your production system and requirements. Our atmospheric copper brazing furnace ensures the consistent quality of our modular adapters and hose fittings. The added support of our in-house tube bending and zinc plating plant enables us to effectively respond to our customers’ individual needs.”
“We focus on manufacturing customer specific, machined components, and specifically turned and milled components and we can produce upwards of 10 million components per annum. To machine that amount of components you have to be experts in the fields of repetitive, medium to high-volume machining, innovative product design and optimised manufacturing processes, as well as understanding and managing the supply chain.”
Lean manufacturing “The platinum and gold mining industry is key to our production output. But globally, businesses are under pressure to reduce costs wherever possible and we have streamlined all our operations to ensure that we can offer products that are highly cost competitive. This has earned us a good reputation in South Africa, which is now opening doors for us further afield.”
“The industries we have expanded into are automotive and rail. For example, on the automotive side, we machine control arms and bushes used on the Ford Ranger, all supplied through tier 1 suppliers. We also constantly produce various suspension components, at volume, for 1st and 2nd tier automotive suppliers.”
Most of the new DN Solutions machines are fitted with an Iemca Advantage series bar-feeder
“On the rail transport side, we now machine 702 components used on the PRASA coaches. This might sound like a fair amount but it only represents 0.26% of the components used on a coach. We are also involved in bogie machining.”
“Despite what we thought was an optimal machining facility a recent lean assessment commissioned by the Automotive Supply Chain Competitiveness Initiative (ASSCI) highlighted a strong operational skill-set at Wekaba but there were some gaps in terms of the foundation and understanding of Lean manufacturing.”
“According to the assessment it was evident that elements of Lean methodologies had been applied in most areas but there was clearly a gap in terms of a focused Lean initiative. A clear example being a mindset of housekeeping in all plants but little to no understanding of 5S and its benefits. It was clear the initiative needed to focus on training but also on providing a structured approach to Lean.”
“The main project focuses were to provide clear training on the foundation of Lean, implementation of certain Lean foundations, and develop and maintain a continuous improvement methodology.”
Additionally, we have purchased a TongTai QVM 610AII vertical machining center that was supplied by PBS Machine Tools
“It was also noted that most automotive customers required IATF certification and Wekaba Engineering required assistance to reach IATF accreditation. This was added to the scope of the project for the project consultant to assist with providing a gap analysis, supporting documentation and managing the timelines of reaching the accreditation, which should be attained in the first quarter of 2024.”
“Collectively, these activities drove operational improvements in the areas of implementation over the duration of the project, with both internal scrap rates and production lost to internal materials unavailability improving meaningfully. OEE (Overall Equipment Effectiveness) increased in all the plants over the project.”
New CNC machines and automotive building “During the whole ASSCI project implementation we had to also apply a mindset change throughout the company. This was not aimed at just the staff on the floor or in assembly and despatch, it was also aimed at management. The result has been significant.”
“Our 125 CNC machines are in various buildings on site. They all operate efficiently because we service and maintain them to maximum output requirements. But they are all old technology as they are several years old.”
An existing DN Solutions machine has been moved to the new building
“Additionally, they are mostly restricted to either turning or milling. They include Hyundai Wias, Leadwells, Hitachi Seikis and Doosans, all from multiple suppliers. This was the strategy of the company at the time.”
“However, management has a positive approach to capital investment especially as we have won a few more contracts in the automotive industry. It took a while to implement and the pandemic did not help. But our new strategy began once we had acquired a new building behind our present facility after a protracted negotiation that was complicated with estate requirements with the previous owner.”
“It gave us the blank canvas we wanted. The new asset has 1 000m² of factory space and 600m² of admin and warehousing space. We refer to this new building as the automotive building because it is processing components for the automotive industry.”
“The next decision was the CNC machining deployment we wanted to follow. If you want to streamline production and be competitive in the industry, you will need far more than a standard three-axis CNC mill or a two-axis CNC lathe and a few measuring tools. In a job shop and machine shop world, the components they’re making are often going somewhere else to get assembled into something so this could work in their case.”
Wekaba have installed a Wright air compressor, which incorporates all the modern requirements of an air compressor. Besides being super quiet – you can hardly hear it – it is super-fast in getting up to speed. From start, it will in 45 seconds pump the 6 bar pressure needed by all of the machines on the floor. Precious time savings are made as a result
“But in our environment where we are machining 1 000s of many different components daily, it does not work. Historically, single and multi-spindle automatics and rotary transfer machines have been tooled to run specific jobs for extended periods of time. These might drop complete components and fittings every few seconds. Again, this does not work in industries such as automotive and hydraulic where we are involved in.”
DN Solutions’ turn/mill machines “We decided to go the one supplier route and of the 17 new CNC machines we purchased to house in the new building, 15 of them are DN Solutions’ turn/mill machines that have been supplied by Puma Machine Tools. They are made up of the Puma GT 2100 and Puma DNT 2100 ranges and most of them have been supplied with an Iemca Advantage series bar-feeder. This gives you some idea of the type of work they will be doing.”
“We had more work than people to take on, even though we are operating on a double shift system. We needed more cutting hours than one shift could handle and that is why we went to the double shift system. But then it became obvious during the assessment that we needed more product to be produced in a shorter time frame. The solution was to invest in technology.”
Wekaba have also recently invested in two Sino SHL 60P horizontal turning machines that were supplied by Lead Machine Tools
“In most cases one of the new Puma machines will machine the same amount of components as two of our older model CNCs would do in the same time. The solution also allowed us to free up operators so that they could be better utilised.”
“Automation is the next obvious solution, but none of the components Wekaba manufactures justifies dedicated automation cells yet but we are investigating.”
Changing components and minds “Of course, operating the new turn/mills meant more than purchasing the correct accessories. We had to adjust how we approached setup. We also had to look at where the labour is focused on the machines and what skill sets are needed to operate and programme the machines.”
“At the same time, we had to take into account the change in components to be machined. We are winning more and more contracts for the automotive industry and we are now supplying both Toyota and Ford as well as Benteler SA, a large international supplier of assemblies, components and structures to the automotive industry.”
TongTai QVM 610AII vertical machining center Because we had the space in the new automotive building we have moved and installed a few of our existing machines. Additionally, we have purchased a TongTai QVM 610AII vertical machining center that was supplied by PBS Machine Tools. The machine has a double pallet system, which allows us to setup a job while there is one being machined. This machine was available at the time and it gives us the capacity to machine larger components up to 400kgs.”
“As we have embarked on a major campaign to win more automotive work you also have to take into account all the quality assurance requirements. Besides implementing the IATF accreditation we have also constructed a temperature-controlled room within the automotive building. This room houses our CMM and other inspection equipment.”
A general view of the first CNC workshop at Wekaba
“We have also installed a Wright air compressor, which incorporates all the modern requirements of an air compressor. Besides being super quiet – you can hardly hear it – it is super-fast in getting up to speed. From start, it will in 45 seconds pump the 6 bar pressure needed by all of the machines on the floor. Precious time savings are made as a result.”
Sino SHL 60P horizontal turning machines “We have also recently invested in two Sino SHL 60P horizontal turning machines that were supplied by Lead Machine Tools. These two machines have not been installed in the new building – they have been located in one of the first buildings that the company occupied.”
Grinding of components is also done at Wekaba
“Wekaba’s main focus areas are supported by a number of additional services that enable us to undertake more solution-based offerings. These include full design capabilities, we have a full tool room facility, computerised pin stamping / marking machines, and we offer surface treatment such as hardening and various forms of plating.”
Ownership “The Baller brothers ran the company for 31 years before selling a majority stake in the business in 2012 – 80 per cent – to Medu Capital, a professional investment management company with a focus on private equity. Medu Capital has invested in 33 businesses in diverse sectors including retail, general industrials, transport, construction, mining, healthcare, technology, financial services, food and education. Other industrial companies they are currently invested in are South African Roll Company, Copper Tubing Africa and Weir Minerals.”
Wekaba specialises in high-volume components
“The remaining 20% shareholding is held by management and staff.”
“Wekaba Precision Engineering has embarked on a new era in the company’s history and we are all very excited to be part of it,” concluded Sewnarain.
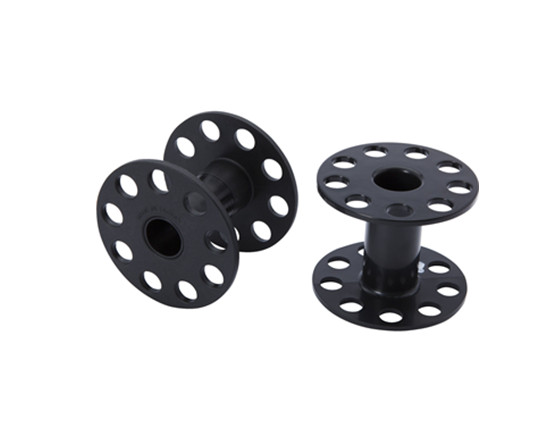
Precision Cnc Machining Services For further details contact Wekaba Precision Engineering on TEL: 011 900 4595 or visit www.wekaba.com