May. 1, 2016 6:00 am, Updated: Mar. 7, 2023 3:28 pm
BURNS HARBOR, Ind. — Despite snow flurries, shippers weren't wasting any time on Lake Superior as the spring thaw set in last month. Aluminum Profile Polishing Machine
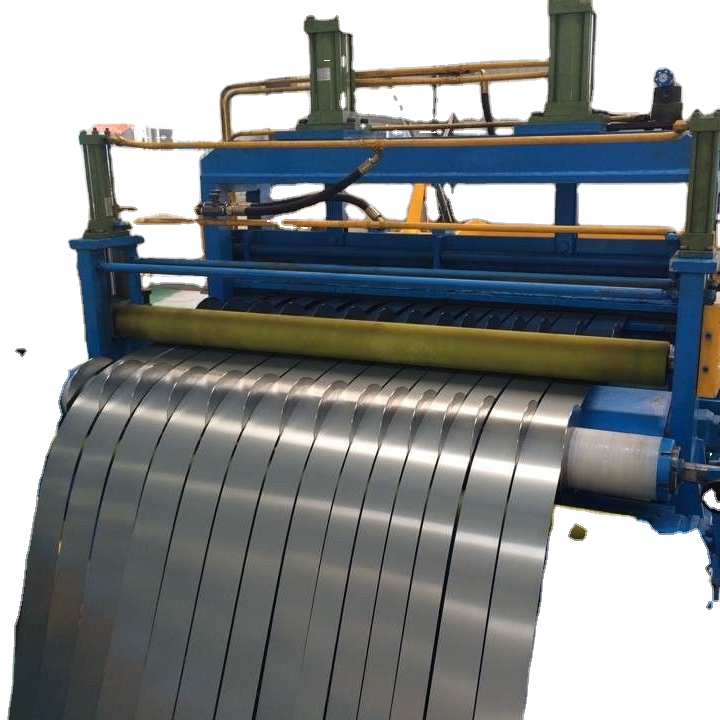
Time is money on the Great Lakes, especially at the end of a long winter when the supply chain slows.
[naviga:h3 style="font-size: 21px; text-align: left;"]Links in the agricultural equipment supply chain
For the two weeks, reporter Brian Morelli will continue to look into how agriculture planters are built. For the second part of the series, Morelli and a photographer visited ArcelorMittal Indiana Harbor in Burns Harbor, Ind.
Mine cart icon by Creative Stall. Steel icon by Pedro Martínez. Factory icon by Krisada. Tractor icon by Bernar Novalyi. All icons from the Noun Project.
By dawn on a windy April morning, conveyor belts moved the last taconite pellets from railcars to the $17 million, 1976-built Joseph L. Block, a 728-foot long shipping vessel, which had arrived at midnight. Hidden between the massive Two Harbors, Minn. port north of Duluth, the Block has capacity for 37,200 tons, and 6.5 hours are needed to load a full ship.
The ArcelorMittal Minorca Mine in Virginia, Minn., in the Mesabi Iron Range about 100 miles northwest of Two Harbors, exports 9,000 tons daily of taconite pellets, which are a manufactured iron composite. The pellets are rust-colored, uniform-sized compressed rocks about the size of a mini candy bar designed for blast furnaces used to make steel.
They also are the ideal size for shipping from Minorca via the Canadian National rail line to ore docks on Lake Superior, and then on freighters to mills on southern Lake Michigan.
The Iron Range produces 40 million tons of iron ore a year — the vast majority of domestic production in the United States. It's the backbone of a variety of products, including agricultural equipment such as the Williamsburg-based Kinze Manufacturing model 3600 planter familiar in its blue paint that can be seen this month crisscrossing farm fields in Iowa and around the world.
The main material, iron, for many planters come from the ground in pit mines in the Iron Range, travel hundreds of miles by rail, boat and truck to mills where steel is made and then to steel service centers, which can customize the product for smaller manufacturers, such as Kinze.
Nearly all the ore moves south by boat. Some sprawling freighters span three football fields and can carry 70,000 tons of taconite in the hull. Over winter, shipping often is hobbled as U.S. Coast Guard icebreakers struggle with frozen waters and vessels jockey for position at the 50-year-old Poe Lock near Sault Ste. Marie, Mich., which is the route for 80 percent of cargo up here, according to the Lake Carriers' Association.
The association has been lobbying Congress for years to invest in more icebreakers and to add a second large lock at Sault Ste. Marie, noting ice in the winters of 2014 and 2015 stalled 10 million tons of cargo, costing 6,000 jobs and more than $1 billion in economic activity.
'Lengthy closure of Poe Lock would cripple steel and related heavy manufacturing,' the association's president, James H.I. Weakley, told his members last year.
The Block reached ArcelorMittal Indiana Harbor, one of several mills on Lake Michigan, after four days, and its self-unloading boom swung over a large hopper to drop pellets destine for blast furnace No. 7.
ArcelorMittal, which has its headquarters in Luxembourg, has six U.S. steelmaking plants including two large-scale mills on Lake Michigan — Indiana Harbor and Burns Harbor east of Chicago near Gary, Ind.
The downturn in steel prices, an oversupply of foreign steel and weak demand from some buyers, such as those in the agricultural industry, help explain why the economy here has been struggling. The unemployment rate in the greater Gary, Ind., area has increased from 5.5 percent in October 2015 to 7.5 percent in March 2016, which is about 25,600 people unemployed out of a 343,000 person labor force, according to the U.S. Bureau of Labor Statistics.
Manufacturing jobs overall are down about 1,000 in the past year.
ArcelorMittal reported a loss of $8 billion in 2015, according to the New York Times, and in February idled its 84-inch hot strip mill at Indiana Harbor, although avoided layoffs, according to the Chicago Tribune. Other steel-makers in the area have suffered as well — U.S. Steel, for example, has laid of hundreds in the past 18 months, according to media reports.
'Things are tough right now,' said Larry Fabina, manager of continuous improvement at ArcelorMittal Burns Harbor. '(Manufacturers) can't export, the price of the dollar — there's a lot of reasons.'
The steelmaking process for the Kinze 3600 continues at Burns Harbor, which has about 4,000 salaried and hourly employees, many represented by United Steelworkers Local 6787. The site layout includes a network of roads, railroad tracks, conveyors and giant factories with stacks pouring out steam and smoke. Forests and two natural preserves, including Indiana Dunes National Lakeshore, surround the industrial complex.
Made here are steel slabs, plates, sheets and rolled coils for automobiles, home appliances, U.S. Navy ships, railcars and construction equipment, as well as for agricultural equipment.
See More: Miners work the Iron range in the first step in the agricultural supply chain.
Fabina has worked up the ranks over 42 years, in castor operations, slabbing and the plate mill. Many aspects of the steelmaking process have become automated, he said.
Shipping vessels offload to docks where machines called stacker reclaimers pile mountains of taconite pellets, which are 'reclaimed' onto a conveyor belt feeding two blast furnaces.
Blast furnaces are where the steelmaking process begins in earnest.
A binding agent called sinter, limestone, which removes impurities, and coke, which is a high carbon material from refined coal, combine with the taconite in blast furnace C and D. The consistency of the coke is essential to the process, Fabina said.
'If you have coke that crumbles, that'll be a problem because it gets so compacted you can't get good flow of air and gases upward,' Fabina said.
The materials are fired at 4,000 degrees Fahrenheit to become metal, although not yet steel. The iron separates from the ore, while impurities and slag, or waste metal, are removed.
Red molten iron pours from the blast furnace into 'bottle cars,' which run on short rail lines to a steel making facility. Sulfur is added to draw out more slag.
The bottle car tips into a bucket the size of a motor vehicle. A crane from the ceiling more than 100 feet up descends and lifts the bucket across the factory to the basic oxygen furnace to mix with scrap metal. A lance blows oxygen into the mix causing an explosive reaction that sends sparks flaring. The oxygen reduces the carbon content to produce steel.
On this December day, Gary Gabelman, an operator, observed from a pulpit high up in the factory, reading monitors displaying levels of iron, carbon, slag, oxygen and different alloy additives used to customize steel for end buyers. Too soft and it could bend. Too much hydrogen would make it brittle, and it could snap or puncture, which could be catastrophic for end products, such as bridges or boats.
'You have to watch closely,' Gabelman said. 'From the moment it tips out from the furnace, we need to make sure the metal is good, and make sure everything is flowing properly ...
Within 80 minutes we want the ladle open for the next batch.'
The goal is 50 batches of 300 tons of steel every 24 hours, or about 15,000 tons of steel per day.
The liquid steel is poured into a castor where it 'freezes' into a slab at 2,880 degrees. The slab is reheated to become pliable, cut into 30-foot-long pieces with a blow torch, then slides into a hot rolling mill at about 2 mph where it is stretched into a 3,000-foot-long ribbon — now moving 36 mph — is cooled under water and rolled into a coil for transportation.
Other slabs are turned into plates, depending on the end need. Kinze in Williamsburg will use both products for its equipment.
Only about 11 percent of the steel produced at Burns Harbor goes to original equipment manufacturers, such as large agricultural customers, while automotive manufacturers take about 70 percent. A growing market segment is steel service centers, essentially middlemen, that buy large volumes of steel and sell to smaller customers, such as Kinze.
'This facility is so big, there's a lot of small guys that can't buy the volume, so they go to a service center,' Fabina said. 'The bad part about a service center is they will buy from anyone. Today we are getting drastically hurt by imported steel from China, Turkey, Korea they will bring into the United States so cheap and the service centers are trying to make money, so they suck our price down at the same time they fill up their warehouse with foreign steel.'
Major direct-sale customers tend to maintain relationships through good and bad times, he said.
For the Kinze 3600, the next stop is one of these service centers, Steel Warehouse in South Bend, Ind.
Randy Parsons, Steel Warehouse director of steel procurement and logistics, said the service centers feel the pinch from both ends. When business is slow, parts of the plants get idled or the third shift is shut down, he said. Steel Warehouse works to please large customers, but it lacks the size to have much leverage with the large steel-makers. Parsons said about five companies, including ArcelorMittal, make 80 percent to 90 percent of the steel in the United States.
'We are a significant buyer of steel, but we have to be someone good to do business with,' Parsons said.
Tim Morrow, the plant manager, oversees operations. A steady stream of semi trucks — 130 to 160 per day — flow in and out of the grounds with thousands of pounds of steel. The site include 562,000 square feet of 'under the roof' warehouse space, which is important to help protect the steel from rusting.
The name of the game here is constant flow and little downtime, Morrow said. He constantly observes monitors displaying average waste, downtime and operation times for the hour, day and month.
'We can't to afford to have them wait,' Morrow said. 'If the trucks wait more than an hour, my screen flashes red.'
Steel Warehouse, which began in 1947 in South Bend and has grown to 12 locations and 600 employees, tests the steel upon arrival for quality, rust and defects. One of the value-adds Steel Warehouse provides is 'pickling,' which is a process to remove scaling that cause rusting or spoiling. Steel coils weighing up to 65,000 pounds are unrolled, bathed in hydrochloric acid, rinsed, hydrostatically oiled and recoiled in one continuous motion at 300 to 400 feet per minute, or about two or three coils per hour.
The steel can be pressed to the desired thickness. It goes through a slitter where the width of a steel band, which can be 72 inches wide, is broken to the appropriate size for the end customer.
As the steel is recoiled, operator Hector Hernandez fastens metal straps that prevent unwinding, which could be deadly. The coil then is ready for shipping.
Steel Warehouse has a facility in Rock Island, where products from Kinze are held until orders come in. The company has an in-house fleet of about 50 trucks to buoy trucking needs, which have been stressed by a national driver shortage. The steel is hauled to Rock Island and then on to Williamsburg for Kinze, which receives one to three shipments per day.
'We are always trying to have a good balance of steel to support what Kinze needs to having too much to a point where it would sit and rust,' Parsons said.
Caleb McCullough, Gazette-Lee Des Moines Bureau State Government 50m ago 50m ago
By Gazette-Lee Des Moines Bureau State Government 90m ago 90m ago
Gazette-Lee Des Moines Bureau Campaigns & Elections 4h ago 4h ago
Erin Murphy State Government 1m ago 1m ago
State Government Jan. 29, 2024 3:16 pm 5h ago
Campaigns & Elections Jan. 29, 2024 3:21 pm 5h ago
Erin Jordan Agriculture 2h ago 2h ago
Environmental News Jan. 29, 2024 5:00 am 15h ago
Agriculture Jan. 29, 2024 9:30 am 11h ago
Business News Jan. 28, 2024 5:00 am 1d ago
By Katie Mills GIorgio, - correspondent
Business News Jan. 28, 2024 5:00 am 1d ago
Business News Jan. 28, 2024 5:00 am 1d ago
The Gazette has been informing Iowans with in-depth local news coverage and insightful analysis for over 140 years. Support our award-winning, independent journalism with a subscription today.
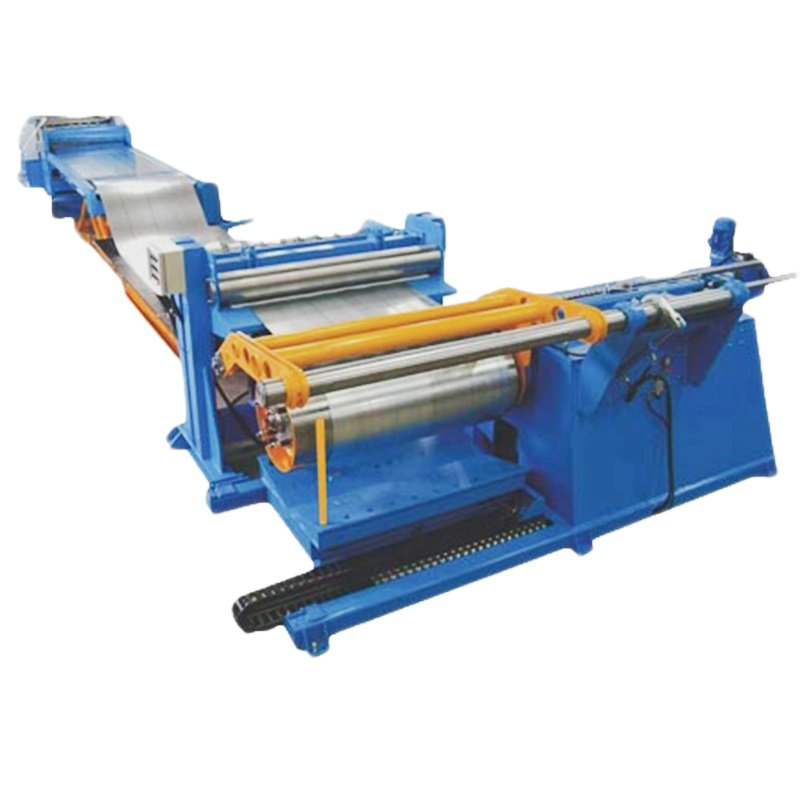
Aluminum Profile Cnc © 2024 The Gazette | All Rights Reserved.