by Larry Landis, Director of Technology and Quality, IDI Composites International and Don Sage, Senior Product Engineer, Owens Corning
Here’s an in-depth look at glass reinforcement strategies that make Structural Thermoset Compounds an excellent material for high-performance applications. Glass Fiber Direct Roving For Lft-D/G
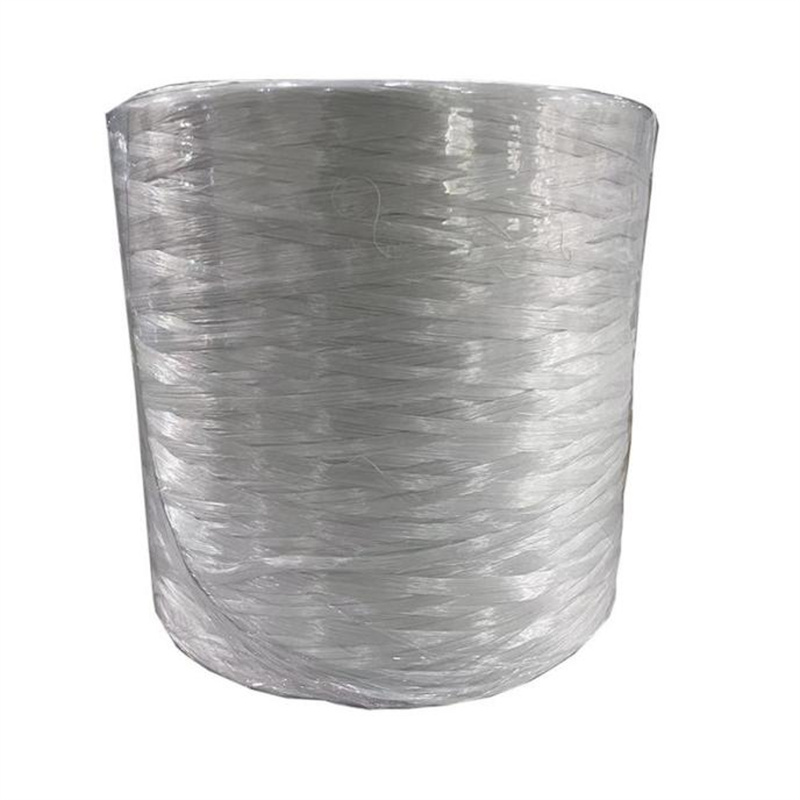
The development of new materials to address the limitations and cost of metals and thermoplastics has led to closer cooperation between resin manufacturers, manufacturers of reinforcement materials, and manufacturers of molding compounds. Because of this cooperation, materials such as structural thermoset compounds can deliver greater strength, lower coefficients of thermal expansion, and better corrosion resistance than other commonly used materials, while increasing design flexibility and manufacturing efficiency. The strong molecular bonds inherent in structural thermosets impart a tight web of inner connectivity that allows these materials to maintain excellent structural properties during prolonged exposure to extreme chemical and temperature profiles. Automotive, military, industrial, electrical, sports, and safety markets rely increasingly on Structural Thermoset SMC (sheet molding compound) and Structural Thermoset BMC (bulk molding compound) to address demands for higher mechanical strength and lower weight and density. Reinforcement strategies are often critical to the structural characteristics that these markets demand.
Thermoset basics Structural thermosets are distinguished from standard thermosets by the use of specialized resins combined with higher levels of reinforcement (glass, carbon, aramid, and so on.). This combination allows structural thermosets to satisfy unique requirements. The added reinforcement imparts additional strength and stiffness, while the special resin formulation protects the fibers and helps the compound achieve its overall properties. These properties can be changed by varying the type and quantity of ingredients. For example, fiber type, length, and mix proportion would change flow, strength, and rigidity; varying resin concentration and type would affect the overall strength along with the heat/corrosion resistance of the compound.
Exposure to thermal energy during the molding process for Structural Thermoset Compounds causes the formation of three-dimensional covalent bonds between the polymer molecules. This process, known as cross-linking, is irreversible. Therefore, cross-linked materials cannot be melted and reshaped. The term “thermoset” accurately describes this chemistry. Cross-linking creates a rigid 3D molecular structure that allows thermosets to maintain the desired physical and electrical properties during prolonged exposure to many conditions, such as high temperature. Thermoplastics, on the other hand, are generally unsuitable for high-temperature environments because they can be melted after solidification. Thermosets have the advantage of high heat distortion temperatures (HDT) and glass transition temperatures (Tg) that literally melt most thermoplastics.
Various properties of structural thermoset composites make this material a good choice for items such as an electrical control switch
Three of the most common thermoset resins are polyester, vinyl ester, and epoxy. Each of these resins has its own price and performance characteristics, so selection is based on application function and cost requirements. For example, you might choose vinyl ester resin for corrosion-resistant products, epoxy for high-strength applications, and polyester when good overall performance and cost are the driving factors.
Reinforcement strategies Many types of reinforcement fiber can be used for structural thermosets, depending on the molding process and the product’s strength requirements. Glass reinforcement options include chopped-strand, mat with random fiber orientation, light textile fabrics, heavy woven materials, knitted materials, and unidirectional fabrics.
Companies such as Owens Corning produce different glass fiber forms for all types of composite materials and conversion processes. Of particular interest to structural thermosets is multi-end rovings (MER), sometimes called assembled rovings, which is the primary glass form used in SMC.
The MER glass product is comprised of multiple discrete bundles of continuous fibers. Depending on the product, each bundle may contain between 50-200 individual filaments bonded together by a sizing or coating. These are wound together into a ball (or bobbin, doff, or tow) and subsequently fed to a chopper that cuts the bundles into 2 in. lengths. Ultimately, these are added to the resin paste to make SMC.
The organic coating applied to the outside of the glass fibers during manufacturing eases glass fiber processing. This coating contains film formers (like PVAC or PE), lubricants, antistatics/processing aids, and a coupling agent – usually a silane – that acts as a bridge, bonding the inorganic glass to the organic resin. The sizing is customized to meet the customer’s specific needs.
In contrast to most other products and processes, the multi-end roving product allows the SMC to flow under heat and pressure and move within the mold more freely, allowing it to fill complicated ribs or details in the final part.
The SMC manufacturing process. Structural thermosets differ from standard thermosets by the use of specialized resins combined with higher levels of reinforcement, such as glass, carbon, aramid. This combination allows structural thermosets to satisfy unique requirements, impart additional strength and stiffness, and help the compound achieve its overall properties.
The most commonly used glass formulation in the composite market is called E-glass, of which there are several products available. Owens Corning’s Advantex® glass is a patented E-glass reinforcement offering excellent corrosion resistance and mechanical properties.
High performance reinforcements, H-glass and S-glass, offer significantly higher tensile strength and flexural modulus for parts with higher mechanical requirements.
Carbon-enhanced reinforcements have a carbon nanostructure that is grown on the outside of a glass strand. This formulation can improve both reinforcing and EMI shielding properties, while addressing the need for further weight reduction.
Why glass reinforcement? Glass fibers serve as the structural reinforcement in a thermosetting resin, the way steel is used in concrete. They have been in existence for decades and have a well-established presence, especially from a product compatibility and performance standpoint.
Glass offers an excellent strength to weight ratio making it and the SMC formulations it goes into a great alternative to metals. The combination of cost, strength, corrosion resistance and weight advantages are the primary reasons to look to composites to replace metal. Many composite applications save up to 50% the weight of a comparable steel part. In addition, mold tooling for composites can be a fraction of the tooling costs for metals.
The two primary mechanical properties of glass reinforcement are tensile strength and flexural modulus. Using the proper glass reinforcement along with the correct resin can yield mechanical properties of a finished part that are comparable to steel, while being lighter weight. This includes tensile strength, flexural modulus, and impact resistance.
There are many variables of the glass fiber product that can affect the performance of the compound and final part. Glass formulation, fiber diameter, number of filaments per bundle, fiber length, and the amount and type of sizing chemistry are all critical.
Glass formulation is important. E-glass is the primary glass used in the most common composite applications, offering superior corrosion resistance while maintaining superior mechanical properties.
Fiber diameter is an important variable that affects wetting and mold flow characteristics. Typically, the larger the fiber, the lower the strength, but the better the wet out. The balance identified in the design of the part and mold will leverage the expertise of the compound provider.
The number of filaments per bundle is a critical variable that impacts mold flow and wetting characteristics. Typically, the construction of the glass is a fine balance between filament diameter and bundle tex (mass density of fiber bundle) to deliver the optimum performance in wetting, flow, mechanical strength, and surface characteristics. The higher the bundle tex, the faster the wet out and the better the flow.
Fiber length is also critical because the longer the fibers, the higher the mechanical properties. However, longer fibers can limit part complexity and design.
Sizing chemistry is probably the most critical variable. The coating should be customized to the application to get better flow and lower scrap rates in compounding and molding processes. The proper sizing can also offer increased UV stability in the final part.
Glass fibers and SMC materials allow flexibility in part design. You have the ability to create parts not possible with a metal. It also allows for part consolidation, reducing assembly and cycle time.
Properly designed composite parts, in general, have a high damage tolerance. Whereas metals can dent, glass fibers and structural composites have high impact strength and are also flexible so that when an impact occurs, depending on the mass, velocity, and part design, the parts will maintain their structural and aesthetic properties without permanently deforming. Various measurements are taken to demonstrate this, such as high rate impact (DynaTup), mandrel bend testing, percent elongation at break, modulus, and fatigue resistance of the finished composite part.
Another example of items made from structural thermoset composites includes this roofing tile.
Structural thermoset SMC and BMC SMC is the primary format for Structural Thermoset Compounds, though some applications require BMC. SMC is a cost-effective, lower weight alternative to many metals. Standard SMC contains 10 to 30% reinforcement, while structural grades are typically in the 40 to 65% range. The reinforcement normally consists of chopped-strand glass fibers measuring 0.5 to 2 in. (12.7 mm – 50.8 mm) long. For most structural compounds, the fiber level exceeds 40%, due to the type of applications in which they are found.
Structural Thermoset SMC manufacturing is a continuous process that combines a viscous paste and glass fiber on a specialized machine with a continuous web. Custom paste that contains the resin and special additives are poured onto a carrier film. Then cut glass fibers are added, along with a second layer of film. This applied paste and glass between a top and bottom carrier film produces a thin “sandwich” that is run through a series of serpentine rollers. The serpentine action and resulting pressure allow the paste to “wet out” the glass fibers. The SMC is then packaged in continuous lengths, 12 to 60 in. wide either on rolls or soft-folded into large, flat containers for handling and thickening. For many applications, the rolls or containers hold in excess of 1,000 lb.
The packaged SMC is matured, typically for 48 hours, depending on the formulation, in a controlled temperature and humidity environment before it is shipped to the customer. This maturation step is critical since the material increases in viscosity over time. Proper maturation allows the finished product to easily peel from the carrier film. Therefore, it is important to tightly control the amount of water and chemical thickeners (metal oxides, metal hydroxides, isocyanates.) added to the paste during manufacturing. Since maturation is an on-going chemical reaction, it is also important to know the optimum molding viscosity window for the best molding performance. Typically, an SMC should be molded within 30 days of manufacture unless it is stored below 75° F. Many molders of Structural Thermoset SMC store their material at sub-zero Celsius temperatures to extend the product’s shelf life.
Though it can be used in transfer and injection molding processes, Structural Thermoset SMC is best suited for compression molding. It can be molded into complex shapes in processes that generate little scrap. With its excellent surface appearance and mechanical properties, it is used as a replacement for sheet metal for heat shields, skid plates, sports equipment, high-strength electrical components, prosthetics, watercraft, and other high-performance products. Due to its ease of handling and sheet size, it is often the only choice for larger parts.
For Structural Thermoset BMC, a resin, fiber reinforcement, and several other ingredients blend to form a viscous, putty-like material. By weight, it normally includes 25 to 40% reinforcement, which usually consists of chopped-strand glass fibers measuring 1/32 to 1/2 in. (0.75 -12.7 mm) in length. BMC is suitable for compression, transfer, or injection molding. When it is injection molded, cycles can be as fast as 10 seconds per millimeter of part thickness. Depending on the application and specific formulation, it provides tight dimensional control, flame and track resistance, superior dielectric strength, corrosion and stain resistance, excellent mechanical properties, minimal shrink, and color stability. Available in numerous colors, BMC also provides surfaces receptive to powder coating, paint, and other coating processes.
Advantages of structural thermoset compounds By evaluating the attributes of structural thermosets early in the design process, custom formulations can be created that take advantage of key material properties for a specific application. Core advantages include:
•Tensile and flexural strength: These compounds have higher tensile and flexural strength per unit weight than most metals. With the high loadings of fiber, their strength allows them to replace many traditional materials. When compared to thermoplastics, such as polycarbonate/ABS, PPO/Nylon 6, and polycarbonate/PBT, Structural Thermoset SMC has significantly higher flexural and tensile strength, depending on the application and reinforcement used. When it comes to high modulus (flex and tensile), they usually yield much higher values than thermoplastics.
These compounds can contain many different resins and reinforcement combinations. Therefore, unlike other materials, they can be custom designed to meet the strength requirements of a particular application. Unlike metals, which have equal strength in all directions, structural thermosets are anisotropic and can be tailored to deliver extra strength in a specific direction. If a thermoset part has to resist bending in one direction, most of the fiber can be oriented at 90° to the bending force to produce a stiff structure in the desired direction. Thanks to their molecular structure, thermosets maintain excellent strength and other physical properties during prolonged exposure to extreme temperatures.
•Dimensional stability: Besides strength, the cross-linked molecules in these compounds provide dimensional stability in high-temperature environments. A thermoset part is far less susceptible to relaxation or creep failure than one made of thermoplastic. The ability to increase fiber content reduces structural variations and makes thermosets ideal for low shrink applications. The dimensional difference between structural thermosets and thermoplastics can be seen during tensile and flexural tests at elevated temperatures. In these tests, thermoplastics may stretch several inches, while structural thermosets stretch just thousandths of an inch. In addition, tensile loads applied in high-temperature environments cause molded holes in thermoplastic parts to elongate over time. Under the same circumstances, however, holes in a thermoset part retain their original shape.
A structural thermoset has a shrinkage range from 0.2% down to zero and, if needed, a thermoset material can expand to be larger than the tool after cooling. Minimal shrinkage helps to ensure close tolerances in molded parts, which often eliminates the need for secondary operations, such as drilling or machining. For many applications, structural thermosets mimic the coefficient of linear thermal expansion (CLTE) of metals, allowing for many types of materials to work together with thermosets in a single application.
•Corrosion Resistance: Unlike common metals, Structural Thermoset SMC won’t rust or corrode when used outdoors or in harsh environments. The material shows long-term resistance to both chemicals and extreme temperatures. A good example of this can be found in chemical manufacturing plants where thermoset ductwork has been in service for more than 25 years. Thermoset compounds have also seen long service life in underground chemical storage systems. The corrosion resistant properties suit applications subject to strict sanitary requirements. Frequent exposure to harsh cleaning chemicals will not corrode the material.
In contrast, thermoplastics can be weakened by corrosive substances and environments. And metals are notoriously susceptible to corrosion caused by water and common chemicals.
•Cost-effective alternative: Structural Thermoset Compounds have a long life span. Many thermoset structures built in the 1950s are still in use. In addition, they have low maintenance requirements. They also reduce manufacturing costs by enabling part consolidation and virtually eliminating final finishing and coloring.
In metal manufacturing, complex designs may require multi-piece parts. The pieces of such a part are made in a series of progressive dies or costly stamping stations and then assembled to create the final product. But by using Structural Thermoset SMC or BMC, complex parts can be made as a single piece in a single step. A simpler process translates into fast, efficient production, with fewer secondary operations, fewer errors, and lower costs. At the end of the manufacturing process, parts made from these compounds are essentially ready to ship to the customer. They require very little final finishing, if any, and benefit from molded-in color and an attractive, durable surface.
•Design flexibility: Normal thermoset molding processes allow complex shapes and intricate details that are impractical or even impossible to produce from metals. And unlike metals, thermosets allow a wide range of material combinations. Various resin and reinforcement options can give unique properties to certain products. In some cases, structural thermosets can be molded on the most basic of systems for R&D and prototyping purposes.
This chart is a comparative look at Structural Thermoset SMC with competing materials.
Applications for structural thermoset compounds The advantages of structural thermosets make them an attractive alternative to metals and thermoplastics in a variety of industries. At present, the primary markets are:
•Military and aerospace: Commercial and military aircraft benefit from structural thermosets in weight, cost, and cycle time reduction; FST retardance; and prevention of galvanic corrosion. Applications include military radomes, ammo handling guides and containers, helicopter components, rifle hand guards, and other weapons components.
•Transportation: A number of exterior automotive components are now made of structural thermosets instead of metals. Thermoset SMC is also gaining popularity among designers of interior vehicle components. The reasons include:
Weight: thermosets are 25-35% lighter than steel parts of equal strength; Dimensional stability: thermoset SMC has a low CLTE and holds up well to engine heat and scorching summer temperatures, making it suitable for vehicle hoods, deck lids, and roof panels; Memory: while metal panels permanently deform on impact, Structural Thermoset SMC panels deform and spring back to their original shape; Cycle time: by reducing the number of parts in finished assemblies, they shorten design and production time. Heat: ability to withstand high temperatures while still maintaining strength is ideal for heat shields and skid plates.
•Safety: These compounds are temperature resistant, fire retardant, and have a high strength-to-weight ratio, which are critical considerations in the safety market. Applications include firemen’s helmets, firefighting equipment components, composite toe caps, and bump caps.
Examples of items made from structural thermoset composites; a safety helmet, roofing tile, electrical control switch, and an M-16 hand guard.
•Medical: X-ray equipment components, instrumentation covers and bases, biohazard receptacles, and prosthetics are just a few of the many medical applications that benefit from the use of structural thermosets. Corrosion resistance, antimicrobial properties, dimensional control, thermal insulation, and dielectric strength make these high-performance materials ideal for the medical market.
•Electrical: These materials hold up well during electrical arching or tracking, with no significant changes to shape or performance. On the other hand, parts molded from thermoplastic materials, often carbonize or melt. Structural thermosets offer comparative tracking index values in excess of 600 volts and dielectric strength of over 15 kilovolts per millimeter. In the electrical industry, they are used for parts with track resistance greater than 600 minutes and arc resistance greater than 180 seconds.
•Industrial: Excellent load bearing capabilities, as well as corrosion resistance and dielectric strength make them the right choice for heavy industrial applications, such as load bearings, valve bodies, and downhole plugs, and components for the oil and gas industry.
•Alternative energy: Each year, the fuel cell industry uses large quantities of structural thermosets to make end caps. They provide heat and corrosion resistance without the shrink or excessive stress that might compromise a thin thermoplastic part. Structural Thermoset SMC and BMC are also suitable for solar power tiles and wind turbines. These applications require materials that won’t warp or deteriorate during long-term exposure to the sun and other natural elements.
•Marine: Structural thermosets provide all the necessary material properties for the Marine market, including corrosion resistance and a high strength-to-weight ratio. Applications include gimbal rings and cowlings, out drive gimbal housing, and power boat seat shells.
IDI Composites International www.idicomposites.com
Browse the most current issue of Design World and back issues in an easy to use high quality format. Clip, share and download with the leading design engineering magazine today.
Top global problem solving EE forum covering Microcontrollers, DSP, Networking, Analog and Digital Design, RF, Power Electronics, PCB Routing and much more
The Engineering Exchange is a global educational networking community for engineers. Connect, share, and learn today »
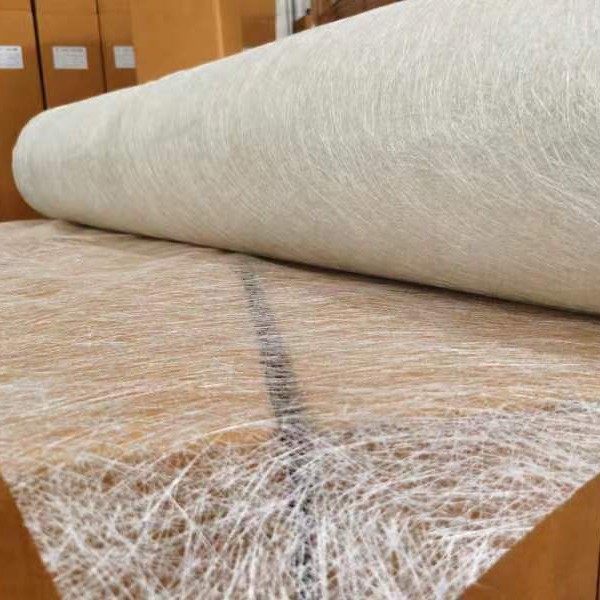
E-Glass Assembled Roving For Smc Copyright © 2024 WTWH Media LLC. All Rights Reserved. The material on this site may not be reproduced, distributed, transmitted, cached or otherwise used, except with the prior written permission of WTWH Media Privacy Policy | Advertising | About Us