The advantages of boric acid-free nickel plating include allowing manufacturers who utilize nickel plating to keep up the ever-changing regulatory policies and support sustainability efforts. #sustainability #regulation #basics
Nickel plating has a vast amount of applications in the electroplating industry. Nickel is needed in electroforming, PCB plating, and nearly all electronic components, either as an intermediate layer or as a final finish. Nickel Pipe

Nickel solutions are very simple to make up. To make up any electrolytic solution, first we need a source of metal, which in this case is nickel. Typically, nickel sulfate would be utilized, even though, depending on the application, it might be better to choose nickel sulfamate. However, for the sake of this article, we will use nickel sulfate as the source of metal of choice.
We then need to add nickel chloride to the solution, to increase its conductivity, followed by a wetting agent, to make sure that the whole surface is thoroughly wetted. Depending on the individual case, different brighteners may be used to improve the appearance and metal distribution of the deposit. The last component in a standard nickel bath is a pH buffer. The vast majority of users prefer boric acid as a buffering agent. We will discuss why this is needed later on.
Let’s look at the amount of metal in the different solutions. We are looking at a rack formulation here as an example. The metal quantities used in electrolytic solutions may vary slightly, but they should be close to the ones in Fig. 1.
Fig. 1 Metal concentration variation depending on the type of metal Photo Credit: Technic
As you can see, the amount of nickel in a standard bath is very different and much higher compared to the other metals, even for solutions that are used in similar applications. For sulfamate baths, the nickel concentration in the electrolyte is even higher.
Users typically want a solution with lower amounts of metal. There are several reasons for this: firstly, most metals are expensive, so the lower the concentration, the less costly it will be to make up and maintain the electrolyte. This is why manufacturers would rather run gold baths with 5g/l (oz/gal) of gold in rack applications than with 20g/l (oz/gal), even though in the second case, the solution would be more stable.
Secondly, if the metal concentration in the solution is lower, the drag out of metal will also be less significant. This means that the wastewater treatment costs will decrease, as well as problems due to the drag in to the positions after nickel plating. Furthermore, metal distribution tends to decrease when the metal concentration in the solution is higher. This is called the “dog bone effect.”
For all of these reasons, it is generally preferable to have lower amounts of metal in any electrolytic solution. However, lowering the amount of metal may also have some disadvantages. One of them is that usually, the degree of current density that can be applied is much lower, reducing overall production speed.
To address some of these concerns, Technic has developed a process called Goldeneye Nickel. With more than 100 installations worldwide, the biggest advantage of Goldeneye Nickel is that it can work with as little as 30g/l (oz/gal) of nickel (Fig. 1) in rack applications. This value is much lower than the standard amount of nickel and more similar to the concentration of the other metals (e.g., copper and silver). Goldeneye Nickel provides all the benefits of a lower metal concentration without the disadvantage of slowing down production. Another benefit of this process is that it can work in high-speed applications up to 40A/dm² (ASF), with only 60g/l (oz/gal) of nickel.
When we explained the making up of the nickel plating solution, we mentioned the use of buffering agents. The standard pH for a nickel electrolyte is around 4-4.5. To understand why we need a buffer, we need to know what happens on the surface of the cathode. While plating nickel in high current density areas, the pH will increase on the surface of the part. In turn, when the pH increases, nickel becomes nickel hydroxide. Nickel hydroxide does not get electroplated, but it will dissolve in the solution afterward. Since we still have voltage, the current is looking for ions to plate; however, since the nickel ion is stuck in the hydroxide form, the only available ion is the hydrogen in the water. Nickel is also stuck in the nickel hydroxide because of a higher pH near the cathode. If the hydrogen gets plated on the part, it will become H2 and be liberated from the solution as hydrogen gas. Therefore, the low amount of ions in the bath is why there might be gas generation in high current density areas. To prevent all of these phenomena from happening, we need a buffer in the nickel bath; the pH buffer prevents the formation of nickel hydroxide by slowing down the pH increase, so more nickel ions are available for plating. As we mentioned, boric acid is widely used as a buffering agent for nickel plating. However, boric acid has some disadvantages.
First of all, in Europe, it has been classified as a dangerous, reprotoxic substance (H360FD) and a “Substance of Very High Concern” (SVHC), which is currently on the “candidate list for authorization.” If boric acid is eventually included in the Authorization List, its use and supply may be severely restricted or banned entirely in the future.
Furthermore, boric acid is a salt and as such, it does not dissolve well in water. The amount of boric acid in the bath is usually around 40g/l (oz/gal), but it is not possible to dissolve more than 60g/l (oz/gal) of boric acid in water. This makes adding boric acid to the tank slightly difficult, as after adding the solid salt, it will be necessary to wait until it is completely dissolved. If the bath cools down, it is even harder to keep it in the solution. If boric acid is not properly dissolved, the deposit on the plated parts will be uneven.
Technic’s R&D team focused on solving these issues, developing a proprietary boron-free liquid buffering agent that prevents the formation of nickel hydroxide (which typically leads to increasing pH in the process, thus decreasing leveling capabilities and brightness) and it does not alter the working pH. Moreover, as removing boron from wastewater can be difficult, using a boric-free nickel solution allows safer, more environmentally responsible wastewater management and reduces overall costs.
Depending on the application, Technic supplies different types of boric-free nickel plating, such as:
Going back to the standard nickel bath components, brighteners and wetting agents are less problematic compared to the pH buffer. Wetting agents can be classified in two ways:
It is pivotal to understand which type of wetting agent works best, depending on the individual applications. Some manufacturers choose to have airflow in their nickel baths; in this case, a non-foaming wetting agent would be the most suitable choice. For high-speed processes in reel-to-reel lines, a non-foaming agent will also be a better option, whereas for applications that only use mechanical movement, a foaming wetting agent may be used.
Brighteners and organic additives are quite simple to use, but it is recommended to periodically purify the electrolyte. Depending on the case, one to four times a year should be fine. Cleaning the electrolyte means getting rid of the breakdown products of the brightener. There are several ways to do this: the easiest one would be to do an active carbon treatment. A more effective treatment would be to remove all the organic additives first with hydrogen peroxide or potassium permanganate, followed by a carbon treatment. Potassium permanganate is a very strong oxidizer and it will break down the organic additives in the bath, so they can be more easily absorbed by the activated carbon.
In conclusion, boric-free nickel plating solutions, such as the above examples from Technic, allow manufacturers who utilize nickel plating to stay one step ahead of the ever-changing regulatory environment around the world, supporting critical sustainability efforts.
T. Laficara, “Navigating Regulation Challenges for “SVHC,” www.technic.com/blog/navigating-regulation-challenges-svhc W. Machu: Metallische Überdecken, Leipzig 1948, p. 402 ff. HW Dettner, J. Elze ( Ed.): Handbook of Electroplating, Vol Surface Finishing, New York 2010, p. 231 ff.
Steffen Habekuss is a Technical Service Engineer at Technic Deutschland.
NASF and its member companies have a long history of environmental stewardship, especially when it comes to PFAS.
Protect parts against rust in efficient, sustainable way.
A guide to lowering pollution and recovering valuable process constituents.
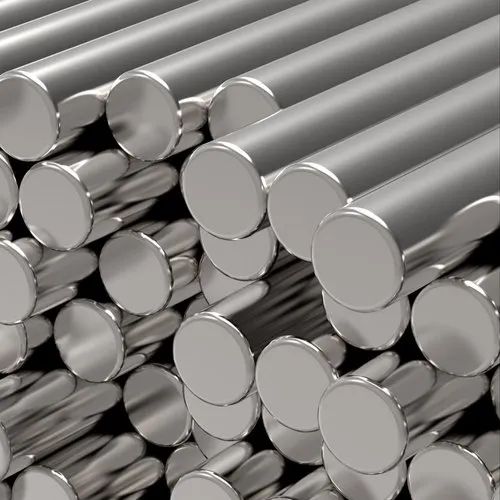
Nickel Welding Copyright © 2024 Privacy Policy [Log On]